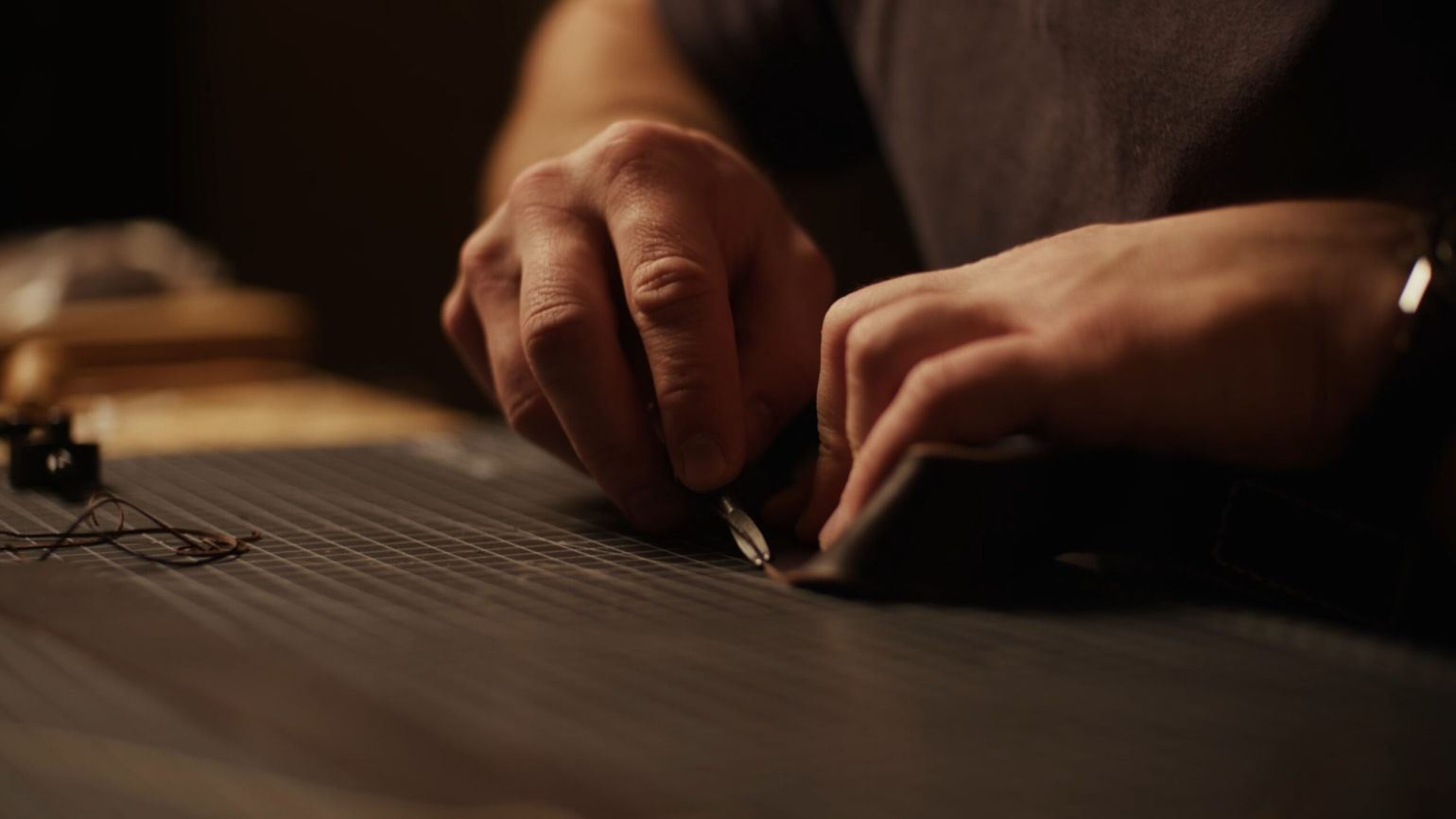
The Art of Leather Crafting: From Raw Hide to Masterpiece
Introduction
Leather crafting is an ancient art that has been refined over centuries. From the raw hide of an animal to a meticulously crafted leather good, each step in the process requires skill, patience, and dedication. Whether it’s a weightlifting belt designed to withstand heavy loads or a stylish wallet built to last, the craftsmanship behind leather products makes them truly unique.
In this article, we’ll explore the journey of leather from its raw form to a finished masterpiece, shedding light on why handmade leather goods are superior to mass-produced alternatives.
1. Sourcing the Leather
The first step in the process is selecting high-quality raw hides. Leather is primarily sourced from cattle, though other animal hides like buffalo and goat can also be used. The quality of leather depends on various factors, including the animal’s breed, diet, and living conditions.
Once sourced, hides go through a preservation process to prevent decomposition before tanning. This often involves salting or freezing the hides until they are ready for further processing.
2. Tanning: Transforming Hide into Leather
Tanning is the process of treating raw hides to prevent them from decomposing and to enhance their durability and flexibility. There are two main tanning methods:
Vegetable Tanning
- Uses natural tannins extracted from tree bark, leaves, and fruits.
- Produces leather that develops a rich patina over time.
- Takes weeks to complete but results in strong, durable leather.
- Ideal for weightlifting belts, straps, and other heavy-duty leather goods.
Chrome Tanning
- Uses chemicals (mainly chromium salts) for faster processing.
- Produces softer, more flexible leather with consistent coloring.
- Commonly used in fashion and upholstery leather.
For premium handcrafted products, vegetable-tanned leather is often preferred due to its durability and natural aging process.
3. Cutting and Preparing the Leather
Once tanned, the leather is inspected for imperfections and then cut into sections based on the product design. The cutting process requires precision to maximize yield and minimize waste. For weightlifting belts, thicker leather is selected to provide maximum support, while smaller accessories like wallets require finer cuts for flexibility.
Cutting can be done by hand using sharp knives or with specialized tools like rotary cutters and leather punches.
4. Hand-Stitching vs. Machine Stitching
The stitching method used significantly impacts the durability and aesthetics of a leather product. There are two primary stitching techniques:
Hand-Stitching
- Uses a saddle stitch technique with waxed thread for maximum strength.
- Each stitch is individually secured, making it resistant to unraveling.
- Takes more time but ensures superior durability and craftsmanship.
Machine Stitching
- Faster and more cost-effective.
- Works well for mass-produced leather goods.
- Can be prone to thread breakage over time.
For premium handmade leather goods, hand-stitching is the preferred method as it provides better longevity and a traditional, artisanal touch.
5. Edge Finishing and Burnishing
After stitching, the leather edges need to be finished to enhance durability and appearance. This involves:
- Sanding to smooth out rough edges.
- Burnishing (rubbing the edges with a slicker tool and friction) to create a polished finish.
- Applying edge dye or wax for added protection and aesthetics.
This step gives handmade leather goods a refined, professional look.
6. Conditioning and Dyeing
Leather is a natural material that requires conditioning to maintain its suppleness. Artisans use leather conditioners or oils like neatsfoot or mink oil to nourish the leather, preventing it from drying out and cracking over time.
Dyeing can also be applied at this stage to achieve different colors and finishes. Some artisans prefer natural finishes that allow the leather’s character to shine, while others apply rich dyes for a bold, customized look.
7. Adding Hardware and Final Touches
For weightlifting belts, bags, and wallets, hardware like buckles, snaps, and rivets are carefully attached. High-quality metal hardware ensures durability and functionality.
Final touches may include embossing or stamping logos, adding decorative stitching, or applying protective coatings.
8. Quality Control and Final Inspection
Before a handmade leather product reaches a customer, it undergoes a thorough quality control process. Artisans check for:
- Stitching consistency
- Properly finished edges
- Leather integrity (no cracks, warps, or imperfections)
- Functionality of hardware components
Only after passing these rigorous checks is the product ready to be sold or shipped.
Conclusion: The Value of Handmade Leather Goods
The process of transforming raw hide into a beautifully crafted leather product is an art form that requires skill, dedication, and time. Unlike mass-produced alternatives, handmade leather goods carry the mark of craftsmanship and attention to detail.
Whether it’s a durable weightlifting belt that supports your toughest lifts or a handcrafted wallet that lasts a lifetime, investing in high-quality leather goods means owning a piece of tradition and artistry.
Are you looking for premium handmade leather gear? Explore our collection and experience the craftsmanship for yourself!